For a consumer, in addition to product quality, sometimes the appearance of the outer packaging also affects their purchasing decision. A beautiful and well-organized packaging will give many positive signals for the quality of the products inside. For plastic bags, the appearance will also determine their life cycle. Many people tend to keep to reuse bags that are thick and have an eye-catching appearance. This is a great success for any business' branding purposes, as bags with their logo or messages are more accessible. The color of the packaging will always be an indispensable factor in achieving such goals.
So how do these plastic bags get the desired color?
Very few of us today think much about colors, because they are so familiar, they seem to be available and surround our lives. If we love a particular color, we can completely equip ourselves with almost everything with that color, from wall paint, furniture to clothes, phones, motorbikes… Maybe we would think more about color, if we knew that people living in the 1900s actually had very little such choice. Most of the pigments that make up the colors around us are discovered after this point.
What is pigment?
Pigments, also known as coloring agent or dyes, are substances that are mixed into materials to change the process of absorbing and reflecting light wavelengths, resulting in their color change. The difference between dyes and pigments is that dyes are water-soluble, while pigments are materials that are almost insoluble. Dyes are also often organic compounds with mild coloring ability, mainly used in the textile and paper industry. Meanwhile, pigments are usually inorganic compounds with high color mixing ability, often used in industries such as paint, plastic, printing ink...
The history of pigments can be considered closely related to the cultural history of mankind, as their use began tens of thousands of years ago, on prehistoric cave paintings. Methods of purposeful pigment production are believed to have developed from ancient times, in Egypt and Babylon. The walls of the temple, as well as the wooden and ceramic surfaces have been decorated with simple inorganic colors created from metal oxides.
Human demand for colorants is growing with higher requirements, leading to more pigments being discovered later. But the synthesis and large-scale production of pigments grew most rapidly only in the last two decades of the twentieth century, because of the increased demand for printing inks for newspapers, coatings for consumer goods, automobiles and plastic products.
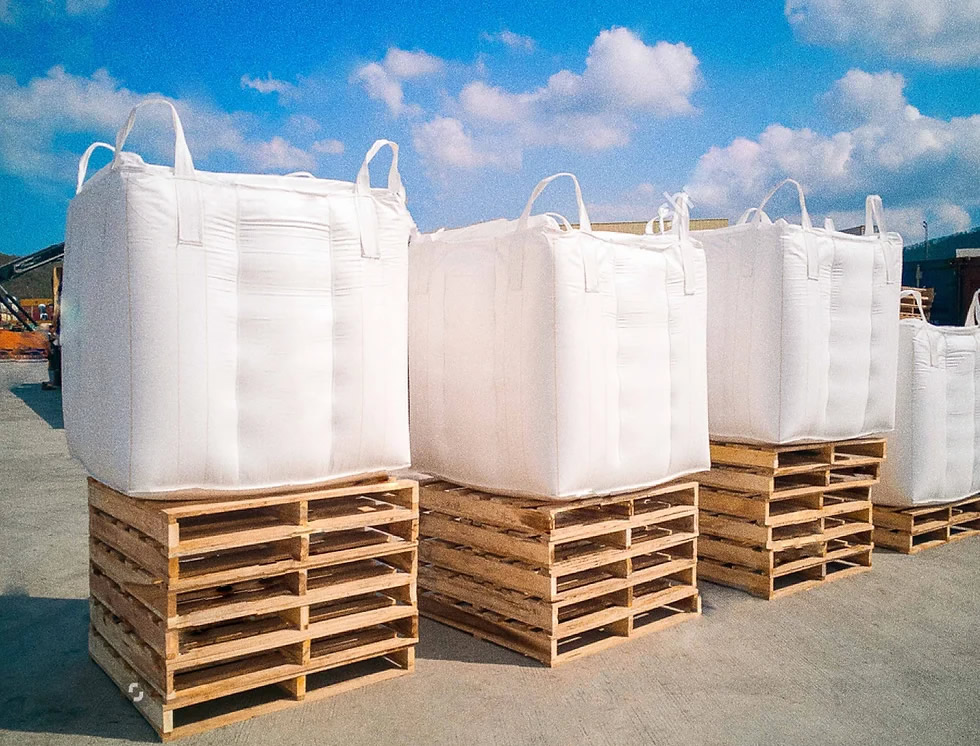
Inorganic and organic pigments
Based on the origin of ingredients in the formula, pigments are classified into two categories including inorganic pigments and organic pigments. With organic pigments, the molecule will have the presence of chain bonds or carbon rings, and are often formed from biological processes. Meanwhile, inorganic pigments do not have the presence of carbon atoms in the structure, and are usually created from geological processes or synthesized from chemical reactions.
Organic pigments
The relatively simple molecular structure with carbon rings or chains makes organic pigments stable and colorfast. Products colored from organic pigments will have bright colors and high gloss. However, they have the disadvantage of being easily decomposed when exposed to solvents or high temperatures. If products using organic colors are left outdoors, exposed to direct light, heat and air, they tend to become dull and disappear.
In the past, organic pigments were mainly derived from natural sources, made from animals or plants, so they were also called biological pigments. These biomaterials go through a simple process that includes washing, drying, powdering and combining multiple ingredients into a formula. But in modern times, these organic pigments are mainly synthesized through organic chemistry, from coal and petrochemical products. Common organic pigments are quinacridone, phthalocyanine, alizarin, azo...
Compared to inorganic pigments, the use of these organics is less frequent, leading to relatively few suppliers in the market and relatively high prices.
Inorganic pigments
If organic pigments represent a product of nature, inorganic pigments represent a man-made product, with formulations mainly coming from laboratories. Such scientifically researched products are researched to have a wide range of outstanding properties, and offer the ultimate range of control to the user. Inorganic pigments can be produced by simple chemical reactions (such as oxidation), which can provide economic benefits on an industrial scale. Inorganic pigments account for more than 90% of the colorant market share, which is estimated to have exceeded the volume of 12 million tons by 2020. However, with an annual output of about 1 million tons, organic pigments are also an equally attractive market.
Most inorganic pigments are more easily dispersed in the material, and colorfast even when exposed to intense heat and light. Most of them are derived from metal oxides or metal sulfides.
How many pigments are there in all?
Taking into account the depth and warmth of the different tones, the number of colors present in nature is immeasurable. The average human eye can perceive about 10,000,000 colors, while a 24-bit computer can display 16,777,215 different combinations of colors. In terms of pigments found and commercially produced, there are currently 27,000 individual varieties listed in the Color Index International data sheet. This is a reference database of color pigments, first published in 1925, by the British Association of Stainers and Colorists. This data is now administered in collaboration with the American Society of Colorists and Chemists, forming the official index of all commercially available colorants.
Unlike other color systems such as Pantone or the Munsell System, the Color Index International classifies dyes and pigments according to their chemical composition, not on the exact value and tint of the color. This helps the Color Index (or pigment code) to tell us exactly what properties and how the pigment will work.
When you purchase pigments or their preparations such as paints, resin pigments, printing inks, ..., you will most likely see this pigment code printed on the packaging label, and they will always have three required ingredients:
The first letter represents the state of the colorant. Solid colorants will be designated by the letter P, dyes by the letter D and S for solvent dyes.
The second letter represents the color: R (Red - Red), Y (Yellow), B (Blue), Bk (Black), M (Iridescent), ...
Followed by the specified number is the ordinal number in which this pigment is recorded and added to the database. The larger number represents the pigment added to the database later, and the largest number in the table represents the most recently added pigment type. Some sequence numbers may be left blank because the pigments in that position may have become obsolete and discarded.
Behind this string of characters there may also be an additional five-digit number (CI code - color index construction number), which represents the exact chemical compound present in the pigment. As an example, Ultramarine blue has a pigment code of PB 29 (Pigment Blue number 29), and construction number CI 77007 (construction number 77007 indicates that this is an inorganic pigment).
It should be noted that paint or pigment manufacturers are not required to disclose which pigments are present in their products. You won't find a pigment code on some proprietary pigment blends, such as Winsor & Newton's Cadmium-free pigments.
Manufacturers can also come up with their own trade names for their products. This leads to the fact that the same pigment can have many different names, for example Monastral Blue, Monestial Blue, Helio Blue, Phthalo Blue, Thalo Blue, Winsor Blue and Scheveningen Blue are all made from the copper Phthalocyanine, which is simply classified by Color Index International as Pigment Blue 15 (PB 15).
Although understanding how pigments work through their formula and chemical composition is extremely complicated, it is quite useful when you want to mix a variety of colors. You can somewhat predict how the pigments will interact when mixed, or which colors will dominate and have stronger coverage, thanks to the color fastness and tinting strength indicators included in the data sheet. In addition, pigment code data also helps you to know whether their chemical composition is safe for food or medical applications, or whether their chemical composition conforms to certain standards or not.
Black pigment
Black pigment has a long history, starting with charcoal paintings in Stone Age caves. Through centuries of research, people have known how to change the burning conditions and choose the type of wood to customize the shade of this black. Coal can be pressed into a dry bar, or it can be ground into a powder and mixed with water or other liquids to produce the black dye that is now known as carbon black, with the pigment code PBk 7.
During the renaissance, artists often worked with black obtained from the soot of oil lamps, known as lamp black pigment – PBk 6. This pigment has a matte black color with a slightly cool tint. The lamp black is also used in Egyptian tombs and murals, replacing charcoal, which is denser but less pure.
Ivory black or bone black was originally created by boiling the crumbs obtained during the ivory making process to remove fat and gelatine, then ground and concentrated into a harder and coarser form to produce black. The production of ivory pigments was stopped in the 1930s, and today the pigment is mainly made from animal bones, with the color index name PBk 9. This pigment is semi-transparent, has a tinting strength is lower than that of carbon-based black pigments, but has a unique feature of deep yellow or brown undertones.
PBk 11 is an inorganic iron oxide pigment, which is different from all the black pigments mentioned above because there is no carbon in the composition. PBk 11 has a very high color fastness and is almost indestructible. In a mixture of colors, it can easily overwhelm all other colors. PBK 11 is also known as Mars black, named after Mars, the god of war in Greek mythology.
The first white substance in history is thought to be natural calcium carbonate chalk, which is an exceptionally soft limestone, formed from the shells and bones of microscopic organisms deposited and compacted over millions of years. The calcium carbonate (CaCO3) that gives the white color can also be obtained from eggshells, oyster shells, ... In European literature, the term "shell white" is often used to refer to these ancient whites. Natural white pigment with calcium carbonate composition is still used to this day, has the pigment code PW 18.
The first synthetic white pigment produced on a commercial scale was lead white (PW 1), which dates back to around 300 BC. Despite its proven toxicity, white lead remained in widespread use until the late 19th century, when the superior zinc white and titanium white appeared and replaced it. There are many documents detailing how to make white lead. In the oldest process, lead rods were exposed to vinegar fumes in sealed clay pots. These pots were buried in manure or tree bark to maintain the temperature for several months so that the lead converted to white lead.
Zinc white (PW 4) with zinc oxide composition (ZnO) is produced by burning zinc in an oxidizing medium or zinc ore in a reducing medium. This pigment has the special property of being able to emit yellow fluorescence under long-wave ultraviolet light. Zinc whites are not toxic, nor are they as clearly affected by hydrogen sulfide as lead whites, but their whiteness is clearly inferior.
In 1908 in New York, a metallurgist named Auguste Rossi invented a brilliant white pigment, titanium dioxide (Titanium White - PW 6). This pigment is extremely stable, it is not affected by heat, dilute acids or alkalis, light or hydrogen sulfide. Most importantly, titanium white reflects about 97% of light, making it the best white ever known. Because of that, it quickly became popular in many fields. Titanium dioxide also provides UV absorption, which greatly improves weather resistance and durability for outdoor applications.
The chemical classification of titanium dioxide, which for many years was considered no problem, is even widely used in the pharmaceutical and cosmetic industries. However, they have become the subject of heated discussion over the past few years, when a European Union authority has changed the way they are classified and evaluated. Titanium dioxide (TiO2) particles with an aerodynamic diameter ≤ 10 μm are considered hazardous when inhaled.
Before titanium white appeared, the dominance in the segment belonged to Lithopone white (PW 5). They once accounted for 60% of the white pigment market, outperforming both lead white and zinc white combined. Lithopone is moderately strong in blends, not as strong as Titanium white, but not as gentle as Zinc white either. For those who are concerned about the durability of zinc white, but don't like the opacity of titanium white, PW 5 can be a good alternative.
Red pigment
Red is a color associated with love, excitement, and danger. This color also symbolizes good luck in many Eastern cultures. There are many red pigments that have been found and present in the pigment database.
The earliest red pigment discovered by mankind was red ocher, which is clay that has been colored by rusted (oxidized) iron. The red iron oxide pigment consists of the mineral hematite with some minor minerals such as clay, chalk and quartz. Red ocher differs from yellow ocher and brown ocher in that they do not contain H2O in their chemical structure. Today, synthetic iron oxide red pigments have the pigment code PR 101. They are chemically very similar to natural red iron oxide (PR 102), but transparent and more vibrant in color.
Lead red (minium) is an ancient pigment that is considered to be one of the first synthetic man-made pigments. Red lead is made by heating white lead to oxidize it at high temperatures. They are still used to this day, in anti-rust paints for steel structures, especially used a lot on ships.
The famous Chinese red color dating back to the fourth century BC is “Chusha” (Cinnabar), which is used to make paints, lacquers, ceramic glazes and calligraphy ink. Many people mistakenly believe that cinnabar is a plant because it is also a medicine in traditional medicine, but in fact, cinnabar is a mineral with the main component mercury sulfide (HgS). Artificial cinnabar, used by the Romans since the Middle Ages. This pigment is named Vermillion, has a color index name PR 106. Vermillion is much more vibrant than natural cinnabar, but both are quite toxic.
Besides the red pigments obtained from minerals, history also records some organic red pigments obtained from plants such as kermes tree, brazilwood or some palm species in Asia. The Incas also had their own red pigment for dyeing their robes, obtained from the Cochineal - a beetle that feeds on cactus.
The age-old reds made from lead and mercury, though toxic, have been commonly used throughout human history. The real alternatives have only appeared for more than a century, with the development of modern chemistry.
Red Cadmium (PR 108) is a dual product of zinc ore. PR 108 can include many different shades of red, for example Cadmium Red Light leans more towards orange, while Cadmium Red Deep is slightly maroon.
Naphthol red pigments PR 5, PR 9, PR 112, PR 170 and PR 188 are a large group of synthetic organic red pigments. While PR 5 can serve as the primary, medium-tone red in the palette, PR 9 is more of an orange hue. PR112 has a soft bright orange color, PR 170 includes Naphthol Red Light with an orange-red color and Naphthol Red Deep leaning towards purple.
Alizarin Crimson (PR 83) has a deep, cold red color and has high tinting intensity. Mixing PR 83 with Viridian Blue (PG 18) or Phthalo Blue (PG 7) creates a very deep black. PR 122 – Quinacridone Magenta is a vibrant red with a blue tint that makes them almost purple. The same Quinacridone family also has a red color PR 202 which is a bit greener than PR 122, PR 206 - Quinacridone Maroon has a red color that turns brown, while PR 207 - Quinacridone Scarlet is bright coral red.
Yellow pigment
Of all the pigment groups, yellow is the largest and most diverse because there are many substances in nature that can produce this color.
The oldest yellow pigment in prehistoric cave paintings, is yellow ocher, also crumbly clay colored by iron oxides. They are still in use today, with the pigment code PY 43 for natural yellow iron oxide and PY 42 for synthetic yellow ocher. Both natural ocher yellow and synthetics are both great colors in art, as they will produce very natural looking greens when mixed with blue pigments.
In early civilizations in Asia, Egypt and Greece, human used a yellow substance called Orpiment, which was synthesized by subliming a mixture of sulfur and a small amount of arsenic oxide. The Babylonians used Napoli yellow, which was prepared by heating a mixture of oxides of lead and antimony. Napoli yellow currently has a pigment code of PY 41.
Another well-known yellow is Indian yellow, which is said to be made from the bladder gravel of cows eating mango leaves. However, the original Indian yellow color dating from the 15th century no longer exists. Today's Indian yellow is Diarylide yellow (PY 83).
The 19th century saw the introduction of more modern inorganic pigments such as chromium yellow (lead chromate), cadmium gold (PY 35 and PY 37), nickel gold (PY 53 and PY 150), …
Some other yellow pigments include: Hansa yellow group (PY 3) with bright greenish yellow, PY 65 with deep yellow and PY 97 medium yellow, Barium Chromat lemon yellow (PY 31), Strontium chromate (PY32), cobalt yellow (PY 40), arylide yellow (PY73 and PY74), Isoindolinone yellow (PY 110), Diazo yellow (PY 128), Quinophthalone yellow (PY 138), Benzimidazolone yellow (PY 151, PY154 and PY 154). PY175), …
Blue pigment
Blue includes sky blue and navy blue which are very rare colors in nature. Less than a tenth of plants have this color, and in animals it's even rarer. Even if they're blue, it's not because they actually have a blue pigment, but they've actually done light tricks to achieve.
In plants, blue color is achieved by mixing or altering natural pigments, most commonly by altering the acidity on red anthocyanin pigments such as in canaries, bellflowers, and hydrangeas.
Instead of mixing or changing pigment, the blue color in many animals is caused by structures on their bodies that are able to change the wavelength of light. For example, the Morpho butterfly is blue because the scales of its wings are ridged, causing light to bend, making the only wavelength of light it reflects is blue. The only exception in nature is the Obrina Olivewing butterfly, the only animal known to have a real blue pigment.
The raw material of mankind's first green pigment was "lapis lazuli", a precious stone originating from mines in Afghanistan. "Lapis" means "stone" in Latin, "lazuli" comes from the Persian word "lazuward", meaning "blue". The blue created from this stone is called Ultramarine Blue, is a most perfect pigment, with its qualities said to be unique and unsurpassable. The color index name PB 29 is assigned to both natural and synthetic Ultramarine blue pigments, but today's natural Ultramarine Blue is actually exhausted. Lapis lazuli contains sulfur anions held in an ordered lattice. These sulfur anions have charged particles that move from molecule to molecule, traveling along the surface, helping to create a spatial effect and a deep blue color.
The synthetic blue pigment Ultramarine was discovered in 1826 by the French chemist Jean-Baptiste Guimet. He made a pigment chemically identical to lapis lazuli, by heating kaolinite, sodium carbonate, and sulfur. Synthetic ultramarine usually has a warm red-blue color, which is even more vivid than natural ultramarine blue but is not as pure and has the same depth.
Lapis lazuli is very precious and expensive. Faced with the need for an available and affordable blue pigment, the Egyptians invented the world's first synthetic pigment: Egyptian blue. Calcium copper silicate is calcined at extremely high temperatures, producing a blue-green compound resembling glass. When ground into a powder and mixed with a binder, they create a pigment that persists over time.
Across the ocean, the ancient Maya also found their own color of blue: Maya blue. Scientists are all confused about the origin of this brilliant blue color. It was not until the 1960s that scientists were able to determine the origin of this pigment. It is made by mixing a rare clay (attapulgite or palygorskite) with a dye from a plant in the indigo family.
In 1704 in Berlin, the first modern pigment was accidentally discovered by a dye maker named Diesbach: Prussian Blue (PB 27), also known as Berlin blue. Pigments made from iron ferrocyanide quickly became popular, simply because they were much cheaper than the earlier blues.
Phthalocyanine dark blue was first sold commercially in 1935 under the trade name Monastral Blue or Phthalocynanine Blue. This is a transparent, highly pigmented and reliable blue pigment. PB 15 is divided into 2 types: PB 15:1 – Phthalocyanine Blue Red Shade is more red and warmer, while PB 15:3 – Phthalocyanine Green Shade has a shade closer to green.
Mangan blue (PB 33) is produced by heating a mixture of sodium sulfate, potassium permanganate and barium nitrate at high temperature. This pigment is inert, unaffected by light, heat, acids or alkalis. Manganese blue pigment has now been discontinued due to concerns about the environmental impact of the manufacturing process.
The most common blue color is cobalt blue (cobalt aluminum oxide), which includes a range of pigments such as PB 28 which has a slightly greenish blue tint, PB 29 which is a bit darker, PB 35 which is sky blue, PB 36 is blue with a green tint, while PB 74 contains a little bit of red. Various cobalt minerals have been used since ancient times to color glass and ceramics, but the first synthetic cobalt blue pigment was discovered in 1802 by Louis Jacques Thénard. He discovered that the combination of cobalt oxide and aluminum oxide produced a highly stable blue pigment. Of all the blue pigments, cobalt blue is the only one with opacity.
It was not until 2009, more than two centuries after the last blue was discovered (cobalt blue), that humans found a new blue pigment, and also the last blue pigment up to the present time. It was YinMn Blue (PB 86), which was discovered by chance by a graduate student at Oregon State University. This pigment gets its name from the elements within it including Yttrium (Y), Indium (In) and Manganese (Mn).
Green pigment
Green is the most common color we see on earth. Many of us would think that since this is an abundant color in nature, it would be easy to create this color, but the truth is quite the opposite. Humans have actually been searching for green pigments for centuries. Natural green colorants are actually very few and difficult to access. Natural greens often turn brown in a short time.
Fabric dyers for centuries have created green by first dyeing fabrics yellow, then re-dying them with blue. They have to do twice as much work as the other colors, and the slightest mistake in either process will ruin the final result. Achieving a beautiful and consistent green color over multiple dye batches was a real feat in those days.
The first green pigment on earth is said to appear on paintings in the tombs of the ancient Egyptians. They are made from a rare and expensive mineral called malachite. They tend to turn black quickly.
The ancient Romans found a better solution. They soaked the copper plates in alcohol and obtained a green pigment through the weathering of the metal, known as Verdigris blue. Verdigris was used on murals in Pompeii, throughout the Renaissance, and on medieval manuscripts. This pigment remained in widespread use throughout the centuries until new colors such as Emerald green, Cobalt blue and Viridian blue were discovered.
In 1775, the Swedish chemist Carl Wilhelm Scheele invented a method of making green pigment from arsenite, a chemical compound of arsenic. However, their vivid beauty also carries a dangerous poison. One well-known story of this pigment, is that it was believed to have been the cause of Napoleon's death. The wallpaper in his exile room was Scheele's green. This green color is so popular that they are still used, after it became known that they were toxic.
In the late 19th century, a pigment that was both beautiful and toxic similar to Scheele's blue was created, called Paris Green. Due to its vibrancy, this color was especially popular with impressionist artists.
Emerald greens were first formulated in 1814 in Schweinfurt (hence the name Schweinfurt blue). This pigment is made up of aceto-arsenite copper metal. Viridian blue, patented in 1859, is a transparent green chromium oxide (Cr2O3). They are famous for being a cool green with a hint of blue, used by Vincent van Gogh in many of his works. Today, Viridian blue, with the pigment code PG 18, is supplied by 6 pigment manufacturers worldwide.
Cobalt green is prepared by heating a mixture of zinc oxide and a cobalt salt solution. The pigment was discovered by the Swedish chemist Rinmann in 1780, but it was not until the availability of zinc oxide raw materials in the mid-19th century that commercial production of them became widespread. They are also known as Rinman blue or zinc blue. Cobalt green has a wide range of colors from dark to light, for example, PG 19 has a light green color similar to turquoise, PG 50 has a color range from teal to yellowish green...
Another green color, chromium oxide green PG 17, which is dense, opaque and slightly dull, was first produced in 1798. There are now about 20 manufacturers in the world offering this pigment. This is a pretty interesting color, probably the most durable green pigment ever known. PG 17 are also highly reflective in the near-infrared range, like the infrared reflectivity of green plants, making them the primary pigment used in military camouflage paint.
PG 23 earth green, also known as Terre Verte or Verona Green, ranges from blue shade green to golden shade green. Terre Vverte blue looks very natural, transparent and low gradation, made up of siliceous clay and several minerals. The color of PG 23 changes from yellow to blue, green, depending on the geological variation of the raw clay. Since the supply of natural pigments has largely been exhausted, manufacturers today almost exclusively supply Terre Verte blue with alternative mineral pigments such as iron oxide or chromium oxide...
Phthalocyanine Green PG 7, produced by chlorination of copper phthalocyanine, is a smooth green with a hint of blue. It is the most widely used industrial colorant today thanks to its high color fastness, supplied by 60 pigment manufacturers worldwide. PG 36 is also a Phthalocyanine blue but has a more yellow and bright tint. They are also known as Phthalo Green Yellow Shade, which are made by treating copper phthalocyanine with bromine. Both PG 36 and PG 7 contain quite toxic chlorine, but are the most popular colorants thanks to the beauty of color they bring. PG 50 is the next most popular blue, which is also a toxic mixture of cobalt, titanium, nickel and zinc oxide.
Green is a very special color, because although they look very close to nature, often used to represent environmental missions, it is one of the most dangerous and difficult to reach.
Orange pigment
Realgar is believed to be the first orange pigment, composed mainly of arsenic, and has been used since ancient Byzantium. It was not until the 19th century that the development of pigments made from cadmium brought new options for orange pigments. And in the middle of the 20th century, modern organic pigments such as Benzymidazolone orange, Pyrrole, Quinacridone, ...
Some common orange pigments can be mentioned as: Beta Naphthol Scarlet (PO 5) with a slightly orange red color, Monoazo orange (PO 17) slightly inclined to yellow, Cadmium orange (PO 20) warm and bright, orange Benzimidazolone (PO 36) leans heavily towards strong reds, renowned for their excellent vibrancy and lightfastness. PO 62 also belongs to the Benzimidazolone organic orange group, but tends to be slightly more yellow in color than PO 36. Quinacridone (PO 48) is an orange-brown with a slight yellow tinge, Nickel orange (PO 59) transparent and brilliant, …
Purple pigment
In English, there are two words for purple, Violet and Purple, and only the "V" in the word violet is used in the pigment code. The reason is probably because Violet is actually purple, which is part of the visible light spectrum, and Purple is not. This means that when we see “Violet”, we actually see purple. But when we see “Purple”, we are actually seeing blue and red at the same time. “Violet” leans more towards blue, and “Purple” leans more towards red.
It's hard to imagine that our prehistoric ancestors never saw purple, but it's actually a rare color in fruits, flowers, and animals. Because purple is rare, difficult to produce, and expensive, it is considered the color of wonder and mystery, and was also the color of royalty in ancient monarchies.
Tyrian purple is considered one of the most precious ancient dyes dating back to the Middle Ages, made from a mixture of secretions of two species of snails: buccinum and purpura, native to the Mediterranean Sea. The process of preparing this natural purple color requires great patience, and it takes thousands of snails just to dye just the garment. During the Renaissance, when Europeans were exposed to cultures from the New World, they learned how to extract pigments from Cochineal insects to create purple. The carminic acid that this insect produces is crimson, which turns purple when exposed to alkaline substances.
In 1856, William Henry Perkins stumbled upon a new purple color while he was making a medicine for malaria. He quickly registered the intellectual property and commercialized them under the name mauve (Mauveine). This pigment quickly became a trend in high fashion in England at the time.
The color cobalt violet was also announced not long after, in 1859. The pigment was made by precipitating soluble cobalt salts with disodium phosphate, then washing off the precipitate and heating. Today, there are many cobalt violet pigments with distinct hues and properties, for example, pigment PV 14, which offers a color range from purple red to light pink, or PV 49, which is slightly lighter in color than PV 14.
One of the favorite violets on artists' palettes is Ultramarine violet (PV 15), created by heating the Ultramarine Blue pigment with ammonium chloride. Ultramarine Violet provides a unique purple color that is very clean and bright, semi-transparent to visible light and transparent to near-infrared spectroscopy (NIR).
Mangan violet (PV 16), first produced in 1868, is a slightly dull pigment that is useful in reducing hues in blends. When mixed with Viridian green (PG 18) it produces a matte bluish-gray color.
Quinacridone purple (PV 19) ranges in color between smoky purple and bright pink. Another quinacridone violet pigment is PV 42 which ranges from purple-red to bright pink. The quinacridone pigments are all highly pigmented, producing very deep and vibrant purple patterns when mixed with Ultramarine blue.
Dioxazine violets include PV 23 and PV 37, which have a more blue-tint, creating cool blue-violet colors with high tinting intensity. When mixed with iron oxide red (PR 101), it gives a dark brown color.
brown pigment
Although brown can be seen as a bit dull and less luxurious than other colors, in some cases it represents simplicity, strength and reliability.
Natural clay brown substance with iron oxide and manganese oxide composition, also appears in cave paintings dating back to prehistoric times. Natural brown iron oxides have a pigment code of PBr 7, including many shades of brown, fawn, sepia... Pigment code PBr 6 refers to synthetic brown iron oxides.
The ancient Greeks and Romans used a reddish-brown pigment from the ink of many cuttlefish. This organic color has been used by Leonardo da Vinci, Raphael during the Renaissance, and by many other artists up to the present time.
Van Dyck brown is another natural organic pigment, found in brown coal, peat in the ground. Van Dyck brown is known in Europe as Cologne or Cassel soil, which has been largely deprecated since the 20th century. Despite this, the name continues to be used for total brown pigments. modern case. The PBr 42 can reproduce Van Dyck brown by mixing ivory black with Venetian red, or mixing cadmium red with cobalt blue.
Natural brown dyes can also be obtained from walnuts, chestnut shells, maple leaves, beetroot roots, birch bark, coffee grounds, dandelion roots...
More modern inorganic brown pigments can be mentioned such as PBr 8 - Manganese brown with a color range from reddish brown to dark brown, Florence light brown - PBr 9, light reddish brown PBr 11 made from iron magnesium oxide, red-brown disazo PBr 23, yellow-brown Chrome Antimony Titanate PBr 24, dark red-brown Benzimidazolone PBr 25, dark brown Thioindigoid PBr 27...
Other special pigments
Special pigments are divided into two groups: effect pigments (including metallic pigments, luminescent pigments...) and functional pigments (including photoelectric pigments, thermochromic pigments, ...), infrared reflector...)
• Aluminum pigment is a prominent pigment in the group of effect pigments. Aluminum pigments are used in a variety of pigments and paints to provide aesthetic value, luxury and light effects.
• Fluorescent pigments have daylight-gathering properties to create a glow-in-the-dark effect. They can be used to increase the visibility of prints, or create distinctive markings.
• Infrared pigments change from colorless to intensely colored when exposed to the ultraviolet rays contained in the sun's rays or UV lamps. This pigment is extremely effective for printing anti-counterfeiting stamps on plastic packaging.
• Thermochromic pigments, also known as discoloration pigments, produce reversible color changes over different temperature ranges. They are commonly used in printing, advertising, toy and textile applications.
some common blue pigments
Methods of coloring plastic
Plastic coloring agents can be produced with many different methods, shapes, and operating principles. There are a total of four common types of color additives classified by physical shape, including powder pigment- toner, solid colorant- masterbatch, semi-liquid colorant - color paste and liquid colorant. In addition to these 4 color additives, there are also many types of plastic beads that have been pre-mixed with some basic colors.
Dry pigment
Pigment in powder form is the simplest and cheapest colorant, there is no problem in the production process. Just mix it with resin and put it into the extrusion system to create colored plastic products. With fine granules, they are easily dispersed in the mix of ingredients with only simple mixing baths. However, it is this fine particle that gives dry pigments a weakness, that is, they are easily dispersed into the air during processing, polluting the working environment and adjacent production lines. Dry pigments also make it difficult to accurately weigh each batch of ingredients. So, they seem to be more suitable only for small-scale production.
Dry pigment particles can also get stuck on the material hopper without draining all the way down the extrusion shaft, making cleaning the system difficult. Residual pigments, if not completely treated, will affect the color of subsequent batches in an undesirable way.
The dry pigment has the great advantage that it can be used directly to create colored products without going through another heating stage. This helps manufacturers avoid plastic degradation due to repeated heating.
Masterbatch- Concentrated Colorant
Like dry pigments, masterbatch colorants also need to be mixed in the mixing equipment in the right proportions. However, because the pigment has been compressed, the masterbatch concentrate has a lower mixing ratio, and is easy to preserve and store. This is the most convenient and popular plastic coloring additive today. They also have excellent dispersibility, producing products of uniform and beautiful color, but without the worry of spillage, machine and environmental contamination as with dry pigments.
The masterbatch concentrate is made by mixing concentrated pigments into the base resin material, and then heating and shaping them again to become pellets. When used in the production of plastic products, they are melted again, and are diluted to absorb into the entire material mixture. 25 kg bag of masterbatch is able to color 1 ton of plastic resin material.
The small pellet form along with the manufacturer's published mixing ratio makes it very easy for plastic manufacturers to control the colors on the final product as they desire, while eliminating almost completely the weakness of powder pigments. In Masterbatch, the additives and pigments are encased in the base material resin, which is protected from spoilage agents such as moisture, heat and UV rays, thus making it easier to store.
An undeniable disadvantage of masterbatch concentrates is the "thermal history". When manufactured, both the pigment, additives and the base resin material in the masterbatch have to undergo melting and cooling. When used to make products, they have to go through once, maybe even more than, the same heating. Some pigments or additives have mild thermal stability, which may not be able to withstand such a dense heat history.
When using masterbatch, it should be noted that their pigment composition, additives and even their base resin must be compatible with the type of raw resin with which they will be combined. As an example, when you use the masterbatch to color LDPE plastic bags with the extrusion temperature set to 120°C, the additives and the base resin of the masterbatch must also melt at this temperature. Masterbatch not melting or melting too soon will result in a failure in the end. The masterbatch base resin should be a polymer identical to or compatible with the resin to be used.
However, plastic manufacturers do not need to worry too much about this, because the color concentrate is always provided with appropriate identification information as well as its appropriate use conditions and applications. Color masterbatch suppliers also often have technical staff to support users in all cases. Anyway, this is a market with very fierce competition, with a scale that has exceeded 10 billion USD by 2022. There is only one small thing to note that, on small-scale plastic production machines there are the screw length is short, the masterbatch color particles may not have enough time to melt and disperse into the material completely, causing the resin color to be uneven. In these cases, dry pigment would be a more appropriate choice.
The usual mixing ratio of masterbatch to the original resin is in the range of 1–5%, and several types of masterbatch can be used together.
Water-based pigments or semi-liquid pigments- Color Paste
Water-based pigments are made up of pigments, processing additives and dispersing fillers. They are ground and stirred until they become a slightly viscous liquid. Water-based pigment has high color concentration, small particle size, uniform distribution, good color stability. Plastic products are produced with color paste with almost no abnormal ink spots, uniform and bright color.
Water-based pigments are also used directly in the same processing as dry pigments and masterbatches. They both do not produce pollution like dry pigments, and at the same time can solve the problem of poor dispersibility and compatibility of masterbatch.
The biggest drawback today for water-based pigments is significantly higher than the rest. During use, the screw may also slip if the amount of color added is too large. Water-based pigments will appear precipitated when stored for a long time, need to be stirred well before use.
Liquid Masterbatch
Liquid masterbatch pigments are pigment concentrates like masterbatch, but they are liquid and do not have a base resin. Basically, it is quite similar and easily confused with water-based pigments, only different in viscosity.
This liquid masterbatch can be added directly to the blower screw with a peristaltic pump. Doing so allows for highly accurate dosing and the ability to quickly change colors on the production line, without the interruption of machine cleaning. Liquid Masterbatch is often used to create soft, semi-transparent colors for products.
In terms of color creation, it can be said that this is the product line that brings the highest performance. The final product has vibrant color, higher gloss, minimal defects. The mixing ratio of this additive is very low, only 0.1 to less than 3% of the main material. This helps them take up very little storage space. The biggest disadvantage of coloring solutions is the high cost but the shelf life is much shorter than other additives. At the same time, they also need specialized equipment, namely a metering pump to be used.
Pre-mixed plastic graunles
Pre-colored plastic beads are also a way to create colored plastic products, but not as an additive. They are pre-colored resins, with the same concentration (color) of the final products. Plastic manufacturers just put them in the raw material tank without adding any other additives.
This coloring method will give absolutely accurate and uniform color at any time, because that is the color that the resin manufacturer has assigned with modern control devices. This type of resin does not have a wide selection of colors, but only exists in some basic colors.
The method of using pre-mixed plastic granules is only suitable for cases where absolute color accuracy is required, or businesses that have only very few colors on their products. For example, companies that manufacture waterproof membranes for pools use black HDPE resins, or companies that manufacture water pipes only use gray PVC granules. For companies that have many product lines with different colors, using pre-mixed plastic granules will require a very large warehouse area to store many different types of colored plastic granules. This is considered unnecessarily wasteful.
We will also easily confuse pre-mixed primary plastic resins with colored recycled plastic granules. The mixing of colors for recycled plastic granules, in fact, is intended to obscure the surface defects of the product. Their colors are often of very poor quality and have no uniformity. This type of plastic resin is abundant in the market, the price is also very cheap, but mainly serves the secondary market, and should not be considered as one of the methods of coloring plastic.
color masterbatch are the most popular coloring method in the plastic industry
Is colored plastic safe?
A basic knowledge in the plastics industry is that most additives (including colorants) will be of limited use. Almost no plastic packaging manufacturer suggests to its customers to choose colored bags, except in cases where those colors serve essential tasks. Primary plastics such as Polyethylene (PE), Polypropylene (PP) have a pure and simple chemical composition (including only hydrogen and carbon elements), are assessed as safe for human health. To add to their composition any substance without a clear purpose is considered excessive.
But the additives commonly used in plastic packaging include not only colorants, but also others. They have the effect of enhancing the properties of plastic materials such as strength, toughness, and processability. Due to the importance of additives to plastics, many studies have been carried out to evaluate their impact on the performance and safety of the finished plastic. And the results show that incorporation of additives into plastic materials during fabrication often affects rheology, mechanical and optical properties in unpredictable, and sometimes harmful, ways.
In February 2020, the classification of certain forms of titanium dioxide (often used to produce white pigments) as suspected inhaled carcinogens was announced. In September 2021, ECHA (European Chemicals Agency) published new guidance to help companies and national authorities understand how mixtures containing titanium dioxide (TiO2) need to be labeled: "May form hazardous dust by inhalation when used. Do not breathe dust" (EUH212). Liquid mixtures containing at least 1 % TiO2 particles with an aerodynamic diameter ≤10 μm, should also be labeled with the text "Hazardous respiratory droplets may be formed when sprayed. Do not breathe vapor or mist" (EUH211).
The mixing ratio of additives in plastics is usually very low (less than 5%). Many people believe that with this small amount, and under normal conditions, the above additives will still remain in the plastic, it is difficult to convert into a gas or powder form that can have an impact on human health. But no one could have predicted that under special environmental conditions, things would be different. Additives that bind to plastic molecules are inherently unstable, which will be very easily separated under conditions of high temperature, strong light or during decomposition.
There are many other studies studying the effects of plastic additives that are still being carried out and are about to be done. But one thing is for sure, the standards for these additives will be increasingly enhanced to protect human health. Also in 2021, ECHA also published the 25th update of the Reach (stands for Registration, Evaluation, Authorisation and Restriction of Chemicals) regulation on chemicals used in the supply chain and products. In this update, 8 new Substances of Very High Concern (SVHC) were added, bringing the total number of banned substances up from 211 to 219! Medium-chain chlorinated paraffin (MCCP) is also on the list. This is a commonly used substance as a plasticizer and flame-retardant additive in the plastics, rubber and textile industries!
To meet such increasingly high standards, plastic additive manufacturers are also constantly releasing new products with higher performance and safety. But to be proactive, plastic packaging manufacturers will also need to have a better understanding of the main ingredients, and the additives they are using. At the same time there is a basic principle, which is that plastics that come into direct contact with food, pharmaceuticals or any application related to human health, will usually be produced without any additives in the composition.
And a trend that may not be inevitable in the plastics industry is that organic pigments will return to replace modern inorganic pigments, especially heavy metal inorganic pigments such as cadmium or lead chromate.