Food processing plants, industrial plants, or any other unit involved in packaging applications need packaging that functions well. But there is a problem of how to check the quality of the packaging, and how good the packaging is to not increase the cost.
There are a huge number of manufacturers offering plastic bags on the market, and all of them confirm to their customers that they offer only the best. But it is an obvious fact, not all plastic bag factories have the same product quality. There are huge differences in equipment, materials, and manufacturing experience that can lead to significant disparities in the quality of their products. Checking a few specifications of the plastic packaging item you purchase before final payment to the supplier will protect you from erroneous transactions and bad experiences. At the same time, it helps you to make an objective assessment of the quality among the suppliers whom you have chosen.
Even if you think your plastic packaging is good enough, when you've been using packaging from the same supplier for years and the product has never been damaged, packaging testing can still open up great opportunities for cost savings. You can evaluate whether it is possible to ask the supplier to lower costs by reducing the quality of the packaging a little. Saving in order to reduce costs will always be a goal that almost business operating in the manufacturing industry is aiming for.
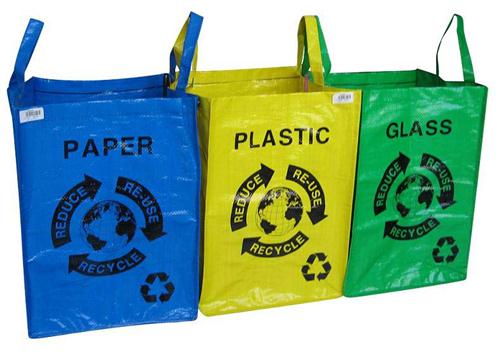
How to know if the plastic packaging that you are using is good or not?
Not only with plastic packaging, quality control of any material or product requires a systematic analysis process. Starting from the quality of the raw materials, the production stages and then controlling the quality of the finished products. However, it is difficult for packaging buyers to access and inspect these production stages. Checking whether the packaging you are using is of good quality comes mostly from the experience during your use of them. However, there are also some methods to help you better control the input quality of plastic packaging that we will share below.
Check the product quality certificate
There are many quality standards for plastic packaging in the world, both in terms of product quality and in terms of machinery and working environment, green standards on environmental impact. The most prominent are the American Society for Testing and Metrology (ASTM) and the International Organization for Standardization (ISO), which are the most trusted organizations in testing and providing evaluation criteria. Many countries also have their own standards such as: JIS standards in Japan, Normes Francaise in France, Deutsche Industrie Normen (DIN) in Germany, British Standards (BS) in the UK... The choice of which standard to use as a criterion for packaging often depends on the market your business targets. To which country your product is exported, it will comply with that country's testing standards. Usually this will be one of the specific requirements in the order.
Regarding the Viet Nam plastic packaging market, we also have our own laws and standards, such as: Standard for commercial packaging, plastic bags (TCVN 5653:1992), standards for testing methods compressive strength for transport and packaging (TCVN 4869:1989), Quality management system (TCVN ISO 9000:2015), Environmental management system (TCVN ISO 14001:2015) ...
The cost of testing and evaluation to get certification is not a small amount, and in fact there are many companies that think they can't afford it, or the benefits are not big enough for them to pay this cost. Tests for packages are mainly carried out when they are exported to markets with very high standards, or the parameters to be tested are of particular importance to the product. To be certified, the manufacturer will send product samples to organizations with testing functions and wait for the results. This means that these certificates are valid only for the sample of the product they have submitted. There is no guarantee that every shipment from a manufacturer will always be of the same quality. Therefore, the test results, although expensive, are only relatively meaningful.
However, quality control is still essential in many cases, especially for packaging used in the food industry. The standard commonly used for this application is the National Technical Regulation on safety and hygiene for synthetic plastic packaging and tools in direct contact with food (QCVN 12-1:2011/BYT), Substances used as basic components of food contact surfaces (CFR 177.1520 FDA).
Check the characteristics of the packaging with test equipment
Mechanical testing of packaging materials is very important, to ensure that they will meet actual environmental conditions, and the products that they protect will reach the end user unharmed. Depending on the application, each business may need different types of packaging, for example, outdoor pallet bags will need UV protection, heavy duty bags will need to be tough and durable, medical instrument bags need to be more resistant to temperatures for sterilization... The above specific characteristics will all have specialized equipment for testing, and on the market there are also versatile testing machines with the ability to evaluate many criteria.
As the trend towards single-use plastic and paper packaging continues to expand, multi-purpose or specialized testers, despite their high cost, are still a worthwhile investment for manufacturers. They can use it to evaluate the functional properties and performance of both the packaging, the raw materials and the final product. Especially as more sustainable recycled materials are developed to replace plastic and paper, it will also be essential to have a tool to fully evaluate their properties to compare them with other materials.
test the tensile strength of the material
In the test, packaging materials are slowly stretched until they break to measure the maximum tensile force they can withstand, and also the final elongation of the material before breaking. This test is an uncomplicated mechanical test and can be performed with any material in sheet or film form. The test is usually performed in both directions: the direction in which the material runs along the machine is called the machine direction (MD), the other direction perpendicular to the machine direction is called the horizontal (cross direction - CD). The reason for such a distinction is because materials can have different tensile strengths in the direction in which they are subjected to the force of impact. Common standards used for tensile testing for plastic films are ASTM D882 and ISO 527-3.
the material is stretched to break in the tensile test
Test for puncture resistance
The most undesirable but often occurring thing is that the packaging is torn or punctured during transportation before reaching the consumer. ASTM F1306 is a widely used standard for testing the puncture resistance of thin film materials. The test is carried out with the upper hanging metal tip fitted with a load cell. This metal end will be pushed slowly down the tensioned test piece by clamping at the ends. The force of impact when the material is punctured will be recorded, and this is the threshold of their resistance to puncture. The average value that is spread over many tests will be used as a criterion for quality control, or for comparison with other materials.
tear strength test
Similar to puncture or tensile tests, this tear test is also one of the most basic ways to assess the strength of materials, with less complicated equipment.
Unlike tensile strength, which simulates the force of stretching action (usually due to load), tear strength represents the ability to resist the force of tearing the film (for example, the packaging got caught in an angle and ripped off). There are several methods of testing for tear resistance, but the most common is to use an instrument called an Elmendorf, which measures the energy required to tear a material.
Tear strength tester elmendorf
check the coefficient of friction
ASTM D1894 and ISO 8295 are standards primarily used to determine the coefficient of friction for thin films or plastic packaging materials. Test performed to establish both static and dynamic friction values for a material when rubbed on itself or on other materials. This index of friction will be closely related to the wear resistance of the material. In the test, a weighted slider is pulled across and over the material under test to determine the coefficient of friction. The friction force is the feedback force against the slider pull generated on the machine. This index is divided by the weight of the slider to calculate the coefficient of friction of the material.
Gas Permeability Tester (GTR) test
If you bring a piece of paper to your mouth and cover it with one hand, then and blow air through them, your hand will feel the hot air escaping from the paper. This indicates that the paper has little or no ability to prevent air from passing through. Although plastic films are known for their waterproofing and airtightness, they actually have the same properties. The only thing is that the permeation rate of plastic film is much slower than that of paper.
The gas permeation rate test measures the volume of various gases that penetrate the packaging material, and is commonly used to test vacuum bags, medical packaging or specialized films. The test is performed by placing the test material in the form of a thin film between two small gas chambers, each of which is subjected to a different gas pressure. One chamber with higher pressure will push the gas through the membrane to the other chamber. The volume of gas that penetrates the membrane represents the gas transfer rate of the material, determined at a given temperature and surface area, in cm³/cm²/min.
water vapor transmission rate test (WVTR)
The water vapor permeability test is similar in principle to the gas permeability test, but the difference is that instead of measuring volume, it is measured by weight. In addition, water vapor permeability measurements are usually measured at equilibrium at a temperature of 38 °C, and a relative humidity of 90%, in grams/m²/day.
water vapor permeability test diagram
gas chromatography test (GC)
Chromatographic testing is a chemical analysis technique in the laboratory to separate a mixture back into its components. For plastic packaging, this test is carried out to ensure that the amount of solvent remaining in the plastic does not exceed 10 mg/dm², according to EU Regulation No 10/2011 plastic materials and articles that come into contact with food.
pasteurization test
Food and medical devices are often pasteurized or sterilized after packaging. Plastic bags used in these applications must be able to be sterilized without the creation of harmful substances, without deformation and changes in properties. The pasteurization test simulates the actual use conditions of the materials to ensure they withstand repeated sterilization cycles (including chemical, steam or gamma radiation sterilization, etc.).
check for anti-fog
This test is performed to determine the anti-fog properties of the material, ensuring that condensation does not form on the inner surface of the packaging material. This test is quite simple, the material sample will be placed in a refrigerator between 7 – 10 °C and monitored for 24 hours.
layer measurement test (Film Layer Analysis)
Multilayer plastic film technology is complex and is widely used in packaging for the industrial, medical and food industries. Multilayer laminates are usually composed of several layers of different materials, each of which provides a unique characteristic such as gas barrier, adhesion, chemical resistance, oxidation resistance, etc. The combination of different layers creates a multifunctional product with outstanding performance.
This layer gauge test is useful for determining the thickness, number of layers that make up the laminate, and for determining the exact material that makes up these layers. Testing will be performed using an energy dispersive scanning electron microscope (SEM-EDS) or an optical microscope (OM). Although energy-dispersive spectroscopy has a much higher level of detail, optical microscopy is particularly useful when performing color film analysis. Optical microscopy is also often used as a premise to identify certain focal areas on a specimen, before using energy-dispersive scanning electron microscopy for further analysis.
Simple ways to check the quality of plastic bags without equipment
In addition to checking the quality certificates obtained by the supplier, you can still perform some simple checks on each shipment without needing expensive machines or sending them to the laboratory. Of course, these plastic bag quality inspection tips are only sensory and relative, but you can absolutely apply them if your packaging requirements are not too special.
check the outside appearance of the bag
Expose the bag to direct sunlight and check whether the surface texture, transparency or color is uniform. If the surface of the bag has irregular clarity or spots with unusual textures and colors, it is likely that they have a high percentage of recycled plastic in the source material.
Look at the bag at a reflective angle to observe the gloss of the plastic surface Plastic that is not of good quality will have a non-uniform luster, even irregular rough spots. The gloss and smoothness of plastic surfaces can also be tested by swiping your hand over them and feeling.
Check weld quality
Regular plastic bags will have the bottom or side formed by the heat-sealing method rather than being completely solid, and this is the weakest point in their structure. You can tear these heat seals by hand with moderate force, if they are stable or only tear when the body of the bag has been severely deformed, then this weld is of very good quality.
For a more precise inspection, you can inject compressed air into the bag to identify possible defects along the weld. The bag can also be submerged in water while pumping for faster test results.
Test for toughness and tensile strength
Take a plastic bag, cut out a strip of plastic as long as you can about 10 cm wide. Apply force and pull on the plastic strips to see if they are tough or break easily. Good plastic will have considerable toughness and flexibility.
Check the thickness of the bag
The thickness of plastic bags is a leading factor determining their durability and load capacity. It is very important to choose a manufacturer with a negligible thickness error. The tools to measure the thickness of plastic bags are not too expensive and you can completely equip yourself to check the quality of the packaging. When measuring the thickness of plastic bags, it is necessary to measure many points on the bag to check the uniformity. The thickness between the points on the bag, if there is a big difference, will reduce the bag's load and durability significantly. This irregular thickness phenomenon is caused by old or not regularly maintained plastic bag machinery, and can also be due to poor quality raw materials.
The thickness of the bag can also be checked by the method of quantitative weighing, by the formula for calculating the weight of the plastic bag. You can weigh a bag to see if its weight is compatible with the thickness you ordered.
plastic bag thickness gauge
Check the load of the bag
The load test of plastic bags is a method of simulating their actual usage conditions. While this method is quite time consuming, it can save you the trouble of getting your product inside on a large scale.
A sturdy bag is often made to hold more than the intended load. You put your product inside the bag plus another item to make the bag hold more than the actual use condition, then raise and lower the bag 20 times. If the bags pass the test, you can continue to hang them for 4 hours, and then continue for 20 hours. If the bags remain undamaged after this time, then they are absolutely of suitable quality.
For products with fine particles such as rice, rice, and animal feed… the durability is also tested by dropping bags containing products from a height of more than one meter to the ground. This procedure should be repeated at least five times and checked for significant damage. This drop test is intended to ensure that your product is free from drops or damage during loading and unloading.
This load test is quite sensitive and should be done once you are sure that the bag that you are ordering is fully capable of passing them. Most plastic packaging manufacturers only commit to the size, thickness and quality of the source material as the buyer has requested. The load of the bag also depends a lot on the shape and size of the product inside, which will vary greatly depending on the conditions of use. A manufacturer will only admit their product to poor quality when there is at least one other manufacturer's product with the same specifications but of superior quality.
operation check
This test applies to ziplock bags, ziplock bags or mouth masking bags. Operate all buttons, zippers and tapes, opening and closing them repeatedly at least 30 times. If bags can no longer open and close smoothly or lose functionality, they will not pass this test.
check print quality
In this test, we simply stick a piece of masking tape over the print on the bag, then peel it off and check. The adhesive tape remains transparent, the printing area where the tape is applied is not affected which means the ink is of good quality. In a worse case, the tape that is peeled off will lead to ink stains, even a printed image. Obviously, these are poorly printed bags that are incapable of maintaining their fresh image and marketability in the long run.
Print quality is less affected by printing technique, but is often determined by ink quality and film processing. Plastic film produced for printing purposes will usually undergo a process called corona treatment. This process can simply be understood as roughening the plastic film to increase the ability to adhere to the ink and solvent by electric charge. It is these stages that make the printing products of some manufacturers better than others.
Poor quality prints will peel off with just a piece of tape
The above is the information accumulated from the comments and feedback from our customers along with the experience throughout our operation in the plastic packaging industry. Hopefully they will be useful for the process of using plastic packaging for your products, and make your work more and more convenient and developed.